Which Of The Following Best Illustrates Deciding How To Produce A Specific Product: Key Examples
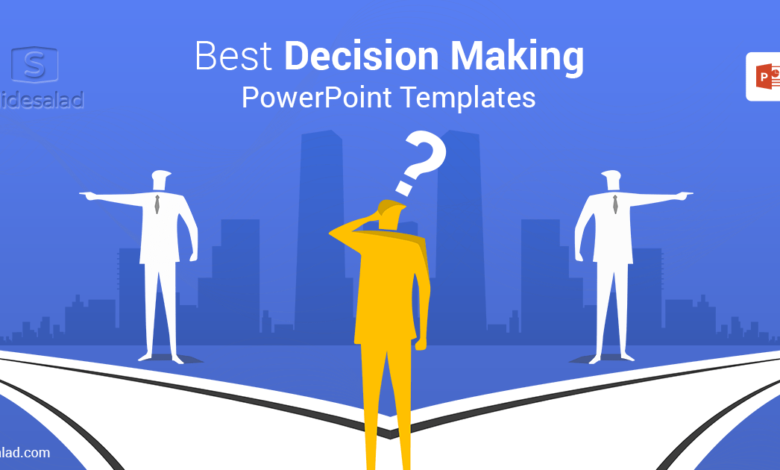
Deciding how to produce a specific product involves several key steps. Each step influences the final outcome.
In the business world, production decisions are crucial. They determine the efficiency and quality of the final product. Factors such as cost, materials, and technology all play a role. Companies must carefully weigh these elements to find the best method.
Understanding these decisions can help businesses stay competitive. It also ensures that products meet market demands and standards. We’ll explore various factors and methods. You will learn how each one contributes to the production process. By the end, you’ll have a clear picture of what it takes to produce a product successfully.
Choosing Production Methods
Choosing the right production method is essential for any business. It affects the cost, quality, and efficiency of the product. There are several factors to consider, including the level of automation and whether to produce in-house or outsource. The following sections explore these options in detail.
Manual Vs. Automated
Deciding between manual and automated production methods involves weighing various factors.
- Manual Production: This method relies on human labor. It is flexible and allows for customization. However, it can be slower and more prone to errors.
- Automated Production: This method uses machines and technology. It can be faster and more efficient. It often results in higher consistency and lower long-term costs. But, it requires a significant initial investment.
In-house Vs. Outsourcing
Another critical decision is whether to handle production in-house or to outsource it to a third party.
- In-house Production: This method gives you full control over the production process. It can lead to better quality control and quicker response times. However, it requires more resources and expertise.
- Outsourcing Production: This method involves hiring an external company to handle production. It can reduce costs and free up internal resources. But, it may lead to less control over the final product and potential communication issues.
Evaluating Cost Efficiency
Evaluating cost efficiency is crucial in deciding how to produce a specific product. It involves analyzing various costs and benefits to ensure the best use of resources. Companies must weigh different factors to make informed decisions. This section will explore important aspects such as fixed and variable costs, and cost-benefit analysis.
Fixed And Variable Costs
Understanding fixed and variable costs is essential. Fixed costs do not change with production levels. Examples include rent and salaries. These costs remain constant regardless of how much you produce.
Variable costs, on the other hand, fluctuate with production levels. Materials and labor are common examples. As production increases, variable costs rise. It is important to balance these costs for efficiency.
Cost-benefit Analysis
Cost-benefit analysis helps in evaluating the potential gains and losses of a decision. By comparing costs with expected benefits, companies can determine if a production method is worth pursuing. This analysis helps in making data-driven decisions.
For a thorough cost-benefit analysis, list all potential costs and benefits. Assign monetary values to each. Calculate the net benefit by subtracting total costs from total benefits. A positive net benefit indicates a viable production method.
This systematic approach ensures resources are used efficiently. It also minimizes risks and maximizes returns. Evaluating cost efficiency through cost-benefit analysis is a key step in deciding how to produce a specific product.
Quality Control Considerations
Quality control is crucial in deciding how to produce a specific product. It ensures the product meets customer expectations and regulatory standards. This section dives into key aspects of quality control considerations, making the process smoother and more efficient.
Standards And Regulations
Following standards and regulations is critical in quality control. These guidelines ensure the product’s safety and consistency. Adhering to them reduces risks and increases trust in the product. It also helps in avoiding legal issues. Companies must stay updated with changes in these regulations to maintain compliance.
Inspection And Testing
Inspection and testing are vital steps in quality control. They identify defects and ensure the product meets quality standards. Regular inspections prevent faulty products from reaching customers. Testing involves checking the product’s functionality, durability, and safety. Proper documentation of these processes is essential for traceability and improvement.
Technology Integration
Technology integration plays a key role in producing specific products. It involves using the latest tools and techniques. This ensures efficiency and quality. By adopting modern technology, businesses can stay competitive.
Adopting New Technologies
Adopting new technologies can streamline production processes. It reduces manual errors. New tools and equipment can automate repetitive tasks. This saves time and effort. It also improves accuracy and consistency in production.
Software And Machinery
Software and machinery are vital for modern production. Advanced software can manage inventory and track production stages. It helps in planning and forecasting. Modern machinery can perform complex tasks with precision. This leads to higher quality products and reduced waste.
Environmental Impact
Deciding how to produce a specific product involves many factors. One key factor is the environmental impact of the production process. Businesses need to consider the effects of their activities on the environment. This includes everything from resource extraction to waste disposal. Understanding and mitigating these impacts is essential for responsible production.
Sustainable Practices
Sustainable practices help reduce the negative effects on the environment. These practices include using renewable resources and reducing energy consumption. Companies can also implement energy-efficient technologies. Sustainable practices often lead to cost savings in the long run. They also improve the company’s reputation among environmentally conscious consumers.
Waste Management
Waste management is a crucial aspect of environmental impact. Proper waste management can minimize pollution and conserve resources. Companies can adopt recycling and composting programs. They can also reduce waste by optimizing production processes. Effective waste management helps in keeping the environment clean and safe.
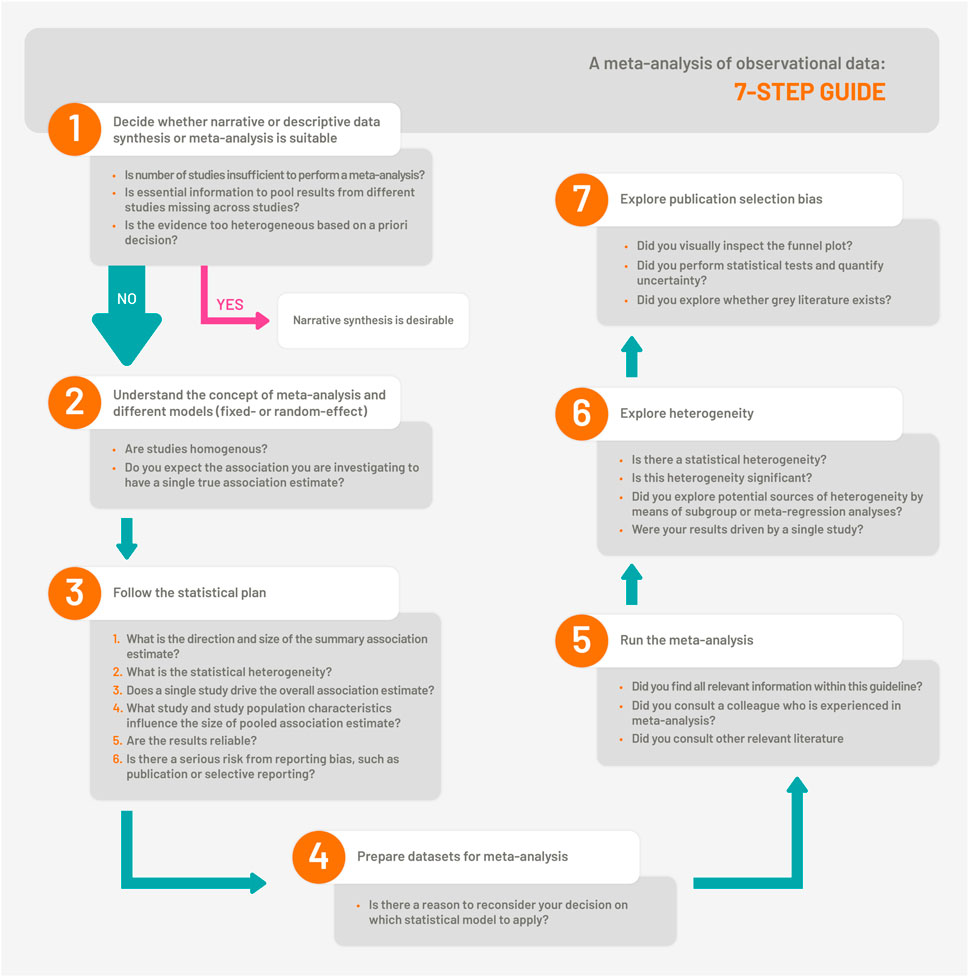
Credit: www.ssph-journal.org
Labor And Workforce
Labor and workforce are crucial elements in deciding how to produce a specific product. The right workforce can significantly impact the production process. This section will focus on key aspects related to labor and workforce.
Skill Requirements
Determining the skill requirements is vital. First, identify the tasks needed for production. Then, assess the skills required for those tasks. Do you need skilled labor or can tasks be automated? Skilled labor often demands higher wages but can result in better quality. Unskilled labor may require less pay but can impact the final product.
Training And Development
Training and development are essential for maintaining a skilled workforce. Training helps workers learn new techniques and improve their skills. Regular development programs ensure that employees stay updated with the latest industry standards. Investing in training can lead to higher productivity. It also boosts employee morale and reduces turnover. Providing opportunities for growth benefits both the company and the employees.
Supply Chain Management
Supply Chain Management is crucial in deciding how to produce a specific product. It involves a series of steps to ensure the product reaches the consumer efficiently. This process includes sourcing materials, logistics, and distribution. Each step plays a vital role in the overall production strategy.
Sourcing Materials
Sourcing materials is the first step in the supply chain. It involves finding reliable suppliers who offer quality materials at the best prices. Companies must evaluate potential suppliers’ reliability, cost, and delivery times. Good sourcing helps reduce production costs and ensures timely production.
Logistics And Distribution
Logistics and distribution are essential for getting the product to the customer. This step includes managing transportation, warehousing, and inventory. Efficient logistics can reduce costs and improve delivery times. It ensures that the product reaches the customer in perfect condition. Proper logistics management helps companies meet customer demands and stay competitive.
Credit: www.gauthmath.com
Market Demand Analysis
To produce a specific product, understanding market demand is crucial. Market demand analysis helps businesses decide how to produce their products. This section will explore consumer preferences and market trends.
Consumer Preferences
Consumer preferences dictate what customers want. Businesses need to know these preferences to create the right product. Customers often look for quality, price, and features. Identifying these preferences involves surveys and feedback.
Businesses can use tables to compare different aspects of consumer preferences. For example:
Aspect | Importance |
---|---|
Quality | High |
Price | Medium |
Features | High |
Market Trends
Market trends show the direction of the market. They help predict future demand. Trends can be identified through market research and data analysis.
Key factors include:
- Technological advancements
- Economic conditions
- Social changes
Staying updated with market trends ensures the product meets current demands. This allows businesses to adjust production methods accordingly.
Credit: www.gauthmath.com
Frequently Asked Questions
What Factors Influence Product Production Decisions?
Several factors influence product production decisions, including cost, resources, technology, market demand, and quality standards.
How Do Companies Determine Production Methods?
Companies determine production methods by analyzing resources, technology, market trends, and cost efficiency to meet consumer demands.
Why Is Cost Important In Production Decisions?
Cost is crucial because it impacts pricing, profitability, and competitiveness in the market.
How Does Technology Affect Production Choices?
Technology affects production choices by enhancing efficiency, reducing costs, and enabling innovative manufacturing processes.
Conclusion
Deciding how to produce a specific product involves many important choices. You need to consider resources, technology, and costs. These factors impact the quality and efficiency of production. Understanding your market is also crucial. The right decisions can lead to a successful product.
Make informed choices and stay adaptable. This ensures you stay competitive and meet customer needs. By following these steps, you can produce a product that stands out.